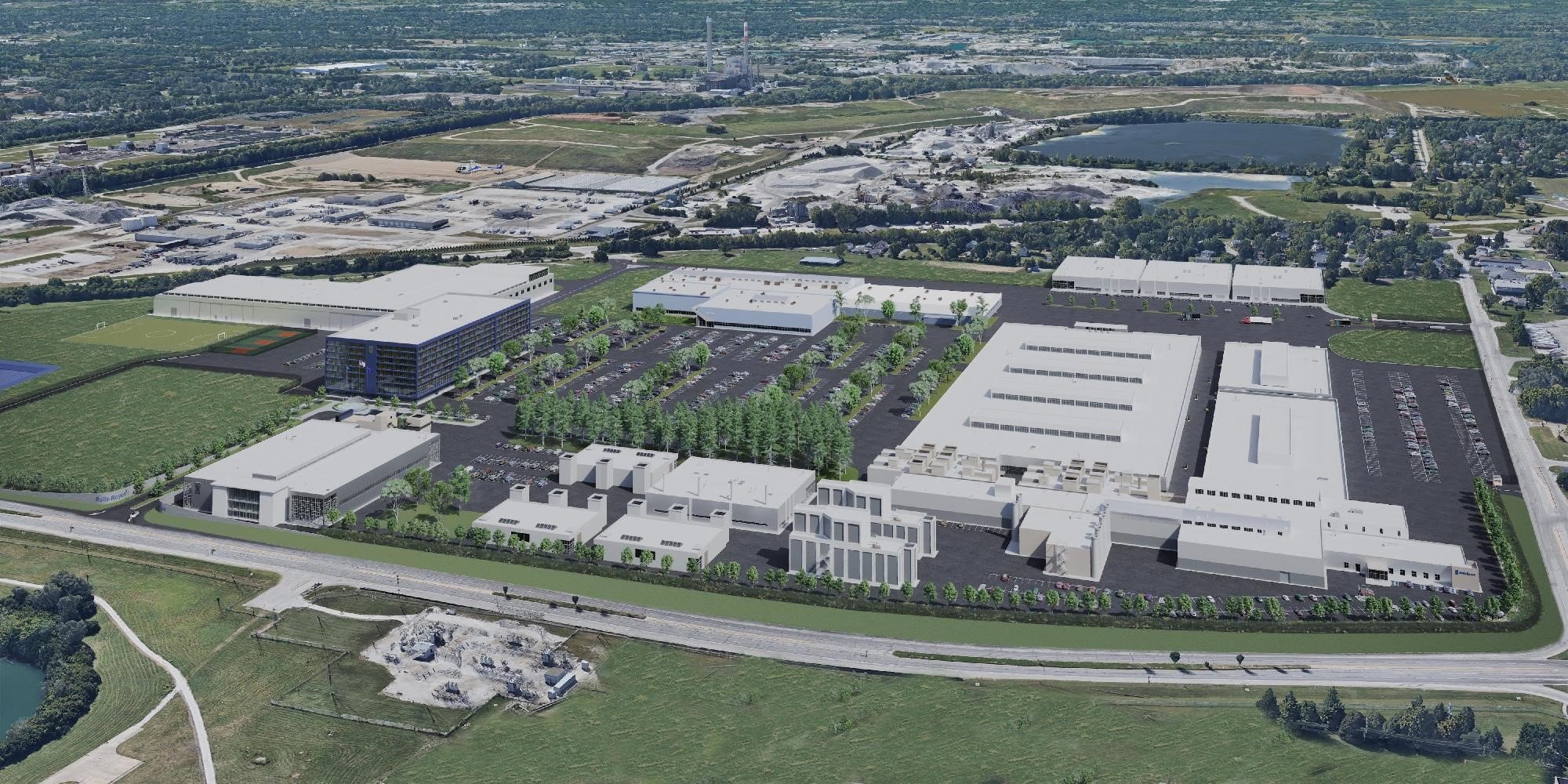
We are the people you can trust to deliver your project on time and on budget.
-
100 MW High-Density DLC Data Center
Conversion of an industrial plant to a 100 MW High-Density DLC Data Center. Our client identified an industrial site as a potential acquisition to convert to a Co-Lo 100 MW Data Center. We have supported our client through due diligence and development of their construction program.
-
240 MW Natural Gas Data Center
We were engaged by the Data Center Owner to develop and deliver a program to convert Natural Gas to the Data Centers primary power source as local grid power was insufficient.
We organized a team to identify turbine solution that was made up of 3 gas turbines and a steam turbine. The advantage of this setup was we were able to move to 55% efficiency and a Heat Rate circa 6.5. This setup reduced fuel consumption cost by more than $25mm per year.
The project also included converting an industrial plant to a High-Density DLC Data Center.
We acted as the Owner Representative through the programming, pre-construction, and project delivery phases of the project.
-
Data Center Site Identification
We were engaged by our client to identify parcels for acquisition that were adjacent to low latency fiber, natural gas distribution, with appropriate zoning.
We researched specific markets and identified properties that met our clients requirements.
We have been engaged to move specific projects from site identification to due diligence and business case development.
-
World-Class Medical Campus
We were engaged to provide project management support through project delivery of a $4.3 billion 864 patient bed downtown teaching hospital complex. The hospital will include 50 operating rooms, 110 care spaces in the emergency department, 3 clinical institutes (cancer, cardiovascular, and neuroscience), and will be a USGBC LEED Silver building.
-
Greenfield Pharma Campus
Albers Management has been engaged to support the delivery of a new $9 billion manufacturing site. The campus will be made up of 12 buildings and will range in size from 3,200 square feet visitor center to a pair of two three story 3330,000 square feet manufacturing facilities. The site will contain administrative offices, lab space, pharma manufacturing, central utility plant, warehousing, and a fire station.
The site is a 600-acre greenfield development project, and the two new manufacturing facilities will produce active ingredients and new therapeutic modalities, such as genetic medicines.
Phase I of the project is expected to be completed within a four-year period (2023-2027). Phase I will be followed by two additional phases where Eli Lilly expects to further expand the campus over a ten-year period for a total cost exceeding $10 billion.
Currently Albers Management is providing project controls and pre-construction services on the project and is engaged to provide project management services through the construction phase.
-
Major Industrial Modernization
$600 mm project involved the subdivision and consolidation of one mammoth manufacturing site into 3 distinct independent facilities. The project included the renovation of 850,000 sf of existing manufacturing space into modern precision aviation manufacturing facilities, labs, and offices. The project also involved the demolition of 1,382,507 sf of obsolete 1940's structures..
-
Canal Walk Renovations
Albers Management was engaged by The City of Indianapolis Department of Metropolitan Development to provide renovations to its Canal Walk on the Indiana Central Canal. The canal was dug in the 1800s and used to improve interstate commerce. Today the canal serves the downtown community as a waterside promenade for walkers, runners, bikers, and sightseers.
Over the years, the canal lighting system had fallen into disrepair; due to the poor lighting of the canal, crime increased in the area and became a topic of debate with local constituents of the City and city services. The initial two phases of the multi-year project, circa $600,000, focused on replacing the existing lighting system with a more energy-efficient, DDC-compatible, higher-lumen output system. Future phases will include canal wall rehabilitation, sidewalk, and artistic improvements
-
Test Capabilities Expansion
Project involves the development of new test capabilities and the modernization of existing capabilities. The project will include constructing new test facilities across multiple campuses, including a Private-Public Partnership, upgrading utility services, and demo’ing obsolete 1940's structures.
Services included requirements capture a business case development, supporting board approval, and providing owner’s representation through the execution of the project..
-
3 mm SQFT Industrial Project
The project included the consolidation and modernization of 3 million square feet industrial campus that included 24 buildings sitting on two adjacent industrial sites across 400 acres. The majority of the buildings were constructed in the 1940s, and many of their major/critical infrastructure were legacy infrastructure and systems from this era. The site had a minor renovation in the late 70’s and early 80’s.
The program aimed to modernize the campus and reduce operating costs by 50%.
Albers Management provided the client Owner’s Representative and Project Delivery services throughout the project.
-
Strategic Planning & Requirements Development
Albers Management worked with the clients' senior executives and PMO office to (a) assess current capabilities against long-term needs, (b) price, identify, and vet options, (c) assess and evaluate options against business needs and operational cost and impact, and (d) develop requirements, based on assessment and affordability, to meet long term business needs. Supported client through the development of their strategic plan and gaining board approval.
With the approved business plan supported client in identifying alternative ownership and funding structures, completing a full requirements document and construction documents, and leading procurement process..
-
New Office Construction & Demolition
Owner’s Representation and Program Management Services for new office construction, demolition and building abandonment at clients manufacturing campus.
-
Power Generation
Provided Project Management Services for client in the modernization of their secondary natural gas power generation system. Services included requirements and business case development and project delivery.
Albers Management support delivered a 30% cost reduction to original Trusted Vendor pricing and further reductions related to right sizing system for actual system demand.
-
Space Utilization Analysis
Provided real estate function support in the analysis of footprint utilization and optimization analysis. Services included space utilization monitoring and data aggregation, data analysis and reporting, and space optimization recommendations. The analysis was the basis of the clients’ long-term strategic footprint plan and catalysis for landlord footprint negotiations and footprint reduction.
-
Facility Condition Assessment, Pre-Construction, & Project Delivery
Engaged in conducting Facility Condition Assessment (FCA) of 1970’s era Ammonium Nitrate Emulsion (ANE) and Ammonium Nitrate Fuel Oil (ANFO). The engagement included:
a) Assessment of the condition of the current infrastructure, mechanical, electrical, and plumbing (MEP) systems, and production equipment
b) Identification of environmental and safety hazards
c) Development of a 20-year capital plan
d) Cost Study for the replacement plant
e) Alternatives analysis
Upon completion of the FCA, Albers Management supported the development of a business case to evaluate alternatives (repair, modernize, and build new). The clients’ board determined that it was advantageous to build new.
Albers Management has been engaged to lead pre-construction services and project delivery of the build new strategy.
-
Compressed Air
Provided Project Management Services for client in the modernization of their centralized compressed air system. Services included requirements and scope development, procurement of services, and project manager through delivery and integration into daily operations.
-
Fire Tube Boilers
Provided Project Management Services for client in the replacement of their steam boiler system and modernization of their steam delivery system. Services included requirements and scope development, procurement of services, and project manager through delivery and integration into daily operations.
Albers Management support delivered a 40% cost reduction to original client design and further reductions related to right sizing system for actual system demand.
-
Wastewater Treatment Plant
Provided Project Management Services for client in the replacement of their obsolete 1-million-gallon water treatment plant to a right-sized and fit-for-purpose system. Services included business case, requirements and scope development, procurement of services, and project manager through delivery and integration into daily operations.
Albers Management identified alternative solutions that reduced the client's headcount by 3 FTE while significantly reducing their environmental and reliability risk. The new system cut water use by more than one million gallons per month. Total client operational savings exceeded $1 million per year.
-
Fuel Farm
Provided Project Management Services for client in the replacement of their fuel farm and modernization of their steam delivery system. Services included business case, requirements and scope development, evaluation of alternative ownership and funding structures, procurement of new system, and project management through delivery and integration into daily operations.
Albers Management support delivered and developed a strategy to reduce current fuel farm size by more than 75% resulting in significant operational cost savings to the client.
-
AHU Upgrades
Removed end of life single supply air fan system and replace with new efficient unit which added heating capability to the unit. Fast-tracked installation to minimize impact to occupants with no downtime.
We relocated and re-connected existing coil to maintain operating temperatures during equipment replacement and added all new electric controls, VFD drives and sensors, all new plumbing, and hot taps for continued service and no downtime.
To drive long-term efficiency and reduce Carbon impact the system was Smart Building Control System with continuous monitoring.
-
Cooling Tower Upgrades
Engaged by client to replace their end-of-life Cooling Tower with efficient and smart-enabled replacement units. The client had additional Legionella standards that required special consideration. As the project manager worked with design engineers to ensure proper sizing and procured the new equipment. Led the demolition and installation activities in coordination with client’s HSE team.
As the equipment was critical to the clients laboratories and clean rooms additional care and planning was taken to mitigate risk of contamination and 100% up-time through replacement.
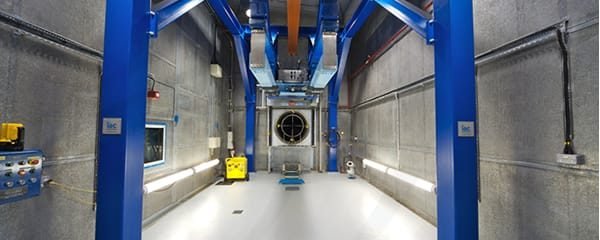